Secondary Batteries (Rechargeables)
Part of Chapter Battery Systems
SECONDARY BATTERIES ARE so named because the original source of the energy they provide is from a second source, such as an ac-powered rectifier, rather than the materials that comprise the battery, as in a primary cell. A much more descriptive name is rechargeable battery. All secondary batteries are rechargeable, while most primary batteries are not rechargeable.
ALKALINE BATTERIES
1.2.1
Alkaline batteries are those that use an alkaline electrolyte, usually KOH (potassium hydroxide). Virtually all commercially available alkaline rechargeable batteries are based on compounds of nickel. The names of the various chemicals used in battery design can be arcane, so bear with us.
Nickel-Cadmium Batteries
1.2.1.1
The nickel-cadmium (or NiCd) chemistry has been around since the late 1800s (when it was developed in Sweden), and accounts for most of the small rechargeable cells sold in the United States, amounting to several hundred million cells each year. Most of these, in turn, are sealed cylindrical cells in the AAA through D sizes with nominal terminal voltage of 1.25 V. Larger flooded (unsealed) cells are used primarily in Europe and other areas, while lead-acid batteries are preferred in the U.S. Also see Large NiCd Batteries below.
In the small sealed cell design, the electrode layers, along with separator layers, are spirally wound (like a jelly roll) within a cylindrical shell. Cadmium metal (Cd) forms the anode (negative terminal) in a fully-charged NiCd cell, with nickel-oxide-hydroxide (NiO(OH)) forming the cathode. The electrolyte is a solution of potassium hydroxide. NiCd cells have excellent high-rate discharge capability and can be discharged to zero volts without permanent damage (although cell reversal should be avoided). They have high power density (about twice that of lead-acid batteries), high cycle life, and good performance at low temperatures. It is this last feature that is valuable in stationary and military applications.
The major disadvantage is the presence of cadmium, a toxic metal. For this reason, NiCd batteries are being restricted in the European Union. Other negative features are a higher cost than lead-acid and a possible “memory” effect (at least for small cells), which may reduce usable capacity in some applications. NiCd batteries have a moderate self-discharge rate.
Discharge Precautions
1.2.1.1.1
A single NiCd cell can be discharged to zero volts without damage, and in fact can be stored in a completely discharged state. Since the KOH electrolyte isn’t changed by the discharge reaction, the specific gravity doesn’t change. The freezing temperature is -25 °C or lower; most large industrial batteries are rated for -40 °C operation.
Discharging a string of NiCd cells that are in series, however, carries the risk of cell reversal (SECTION 1.4.7). Manufacturing tolerances inevitably result in some cells having lower ultimate capacity than others. Those with the lowest capacity in a series string will be discharged to zero first; as the string continues to discharge, those cells will be reversed. Most small NiCd cells will tolerate a reversal of up to a few tenths of a volt, but beyond that, internal gassing may cause permanent damage. To be safe, a series string of cells shouldn’t be discharged below about 0.9 VPC (volts per cell), and certainly not below 0.5 VPC.
Charge Precautions
1.2.1.1.2
Large NiCd cells can safely be charged at the C/4 rate, where C is the capacity in ampere hours. For example, a 100 Ah battery can be charged at 25 amperes, provided that the terminal voltage is carefully monitored. The charge should be terminated when the gassing potential is reached. The cell temperature should also be monitored, since the gassing voltage decreases as the cell temperature increases.
Small sealed cells should be charged at no more than the C/10 or C/20 rate. As the cell approaches full charge, gas is generated internally. The cell is designed so that the negative electrode has a slightly higher capacity than the positive, and this allows the cell to absorb the gas at controlled charging rates. However, internal pressure will increase if the charging rate is excessive. With a high internal pressure, the cell will vent to release the gas. If the vent doesn’t reclose, the electrolyte is exposed to the atmosphere, and the cell eventually dries out, losing capacity. A non-reclosing vent can also leak electrolyte, damaging the host equipment. Repeated overcharge, even with a reclosing vent, eventually reduces capacity and cycle life.
So-called fast chargers for NiCd cells usually have a provision for monitoring cell temperature. NiCd cells have a negative temperature coefficient, so that as the cell heats up toward the end of the charge, the terminal voltage decreases. This increases the charge current, causing more heating, and a vicious cycle is generated (“thermal runaway”). A fast charger that monitors the cell temperature can terminate charging when a critical temperature is reached. A “smart” fast charger can also detect a decrease in on-charge voltage, and terminate the charging to prevent thermal runaway.
Large NiCd Batteries
1.2.1.2
NiCd batteries aren’t limited to portable applications. Large NiCd batteries, up to a thousand ampere hours or more in capacity, are used in industrial applications. In most designs, the electrode materials are contained within steel pockets (the “pocket plate” design), rather than being spirally wound as in small cylindrical cells. Most of these are flooded cell designs, which experience water loss during long-term float charging in stationary applications, due to electrolysis (SECTION 1.5.2.3). To reduce maintenance requirements, some versions are manufactured with pressure vents and excess negative electrode capacity, which help to reduce water loss by recombining the evolved hydrogen and oxygen.
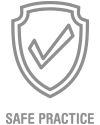
NiCd batteries are extremely rugged, both mechanically and electrically, with long cycle life and long shelf life. They can be stored in a discharged condition. The downsides, of course, are cost and the inclusion of cadmium.
The presence of cadmium classifies NiCd batteries as hazardous waste. All NiCd batteries should be recycled.
Nickel-Metal-Hydride Batteries
1.2.1.3
Nickel-Metal-Hydride (NiMH) cells are the new kid on the block, relatively speaking. Their development was spurred in the 1970s for automotive applications because of their high volumetric and weight energy density, a significant advantage over NiCd. They obviously have the added advantage of eliminating the cadmium.
Characteristics
1.2.1.3.1
Small sealed cells based on NiMH technology are available in AAA and AA sizes. C and D sizes are available, but consumer grade cells are usually equivalent to AA cell capacity, just in larger jackets. The NiMH cells have two times, or greater, the capacity of equivalent NiCd cells. Their nominal terminal voltage is 1.25 V, similar to NiCd, so they can be used as drop-in replacements for NiCd cells. A variety of electric vehicles (EVs), including hybrids, use larger NiMH batteries, up to several Ah, though these are beginning to be outnumbered by lithium-ion batteries.
Discharge Profile
1.2.1.3.2
The nominal terminal voltage on discharge is 1.15 to 1.25 V (depending on discharge rate; the discharge voltage should be about 1.25 V at the C/5 rate, and lower at higher rates). This voltage doesn’t change significantly with temperature, although capacity is reduced at low temperatures (to as little as 20% at -20 °C); by comparison, NiCd cells perform better at temperatures down to -20 °C. At elevated temperatures (up to 50 °C), the discharge voltage and capacity remain nearly constant.
The terminal voltage holds up well until the end of discharge, when it collapses quickly, to about 0.8 to 1.0 V. Since the discharge voltage is constant to this point, the voltage can’t be used to indicate the state of charge. Discharging a single cell to zero volts won’t cause permanent damage to a NiMH cell, but deep discharges of series strings should be avoided.
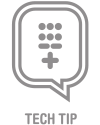
Traditionally, NiMH cells have had a high self-discharge rate, losing up to 50% of their charge in a few months. This performance has been improving as the technology has matured. This effect increases at higher temperatures; it’s a good idea to store charged NiMH cells in the refrigerator if initial capacity is important. Return them to room temperature before putting them in service. In a normal cycling application, the capacity lost through self-discharge is recovered on the first (or maybe the second) recharge.
Because of this self-discharge, NiMH cells are recommended primarily for high discharge rate applications, such as digital cameras. In low drain equipment, such as clocks, service life and shelf life are similar.
In low drain applications, or where long shelf life is required, a better choice might be a primary alkaline-manganese cell, or, for low temperature applications, primary lithium-iron disulfide. NiCd cells could be used if the ability to recharge is important, because of NiCd’s lower self-discharge rate compared to NiMH.
The “memory effect” that may plague small NiCd cells is absent in NiMH cells, so repeated shallow discharges won’t affect their performance in standby or shallow cycling applications. They aren’t particularly suited for standby applications, though, because their self-discharge rate is higher than for NiCd.
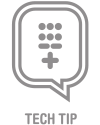
There is a natural variation in the self-discharge rate between cells. Because of this, and the higher self-discharge rate, there is a greater risk of cell reversal when series connections of cells are discharged. As in the NiCd system, even slight cell reversal can cause permanent damage if repeated often. For consumer products, the best practice is to stop the discharge as soon as the battery performance is noticeably degraded.
Life expectancy is no more than about five years due to degradation of the active materials and separators. Cycle life can be 500 discharge-charge cycles or more, provided that proper charging constraints are observed. That’s next.
Charging the NiMH Cell or Battery
1.2.1.3.3
You should not use your old NiCd charger to charge a NiMH cell, unless you are sure that it will charge at the C/40 rate or lower. The best way to charge a NiMH cell is with a “smart” charger, which monitors the cell voltage and temperature to terminate charging when the cell is fully charged. Overcharge can cause severe damage. If you buy a kit of NiMH cells, along with a charger, the charger is designed specifically to recharge the NiMH cells.
Available smart chargers for NiMH cells can recharge a cell completely in two or three hours, far faster than the 12–14 hours required for NiCd. Never use a constant voltage charger. If you use a trickle charger at the C/20 rate or higher, it should be controlled by a timer to terminate the charge after the appropriate time. See Under the Hood below for an explanation of charging requirements.
Under the Hood
1.2.1.3.4
As in the NiCd cell, the cathode (positive electrode) is nickel oxide hydroxide (sometimes referred to as nickel hydrate). The anode is a compound of rare earth metals or transition metals with nickel, cobalt or other metals, using multiple recipes. The metals are reduced to hydrides in the charged state. In this chemistry, a “hydride” is considered to be an alloy of the metal with hydrogen, rather than a molecular compound. The metal recipes are chosen for their unique ability to adsorb huge quantities of hydrogen – many times their own volume.
Like small NiCd cells, small NiMH cells are constructed with excess capacity at the negative electrode. As the cell approaches full charge, the cathode (positive) becomes fully charged first, and starts to generate oxygen. The oxygen migrates to the negative electrode, where it combines with hydrogen to form water. This recombination prevents a dangerous rise in internal pressure. The recombination works, however, only at very low charging rates (C/40 or lower). For continuous trickle charge, some manufacturers recommend rates as low as C/300. For a cell rated 1500 mAh, this translates to a charge current of 5 mA. To avoid a ridiculously long charge time, it makes sense to invest in a smart charger. Read on.
At higher rates, another method of charge termination is required. The end-of-charge voltage characteristic of a NiMH cell has a negative slope, meaning that the on-charge voltage will decrease slightly when the cell becomes fully charged. In addition, internal cell pressure and temperature will rise markedly. A smart NiMH charger monitors the cell voltage and terminates the charge when it detects the negative end-of-charge slope. Some smart chargers also monitor cell temperature, with a temperature sensor built into the battery clip contacts.
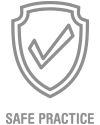
It’s important to limit the internal pressure during recharge. If the pressure rises high enough to vent the cell, the cell loses water from the electrolyte and capacity is reduced. There is also the risk that electrolyte (usually KOH) released through the vent can damage host equipment.
Recycling
1.2.1.3.5
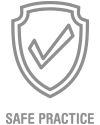
A NiMH cell lacks cadmium, so it’s tempting to dispose of it in normal household (or industrial) waste. If possible, NiMH cells should be recycled, to recover the metallic components. Recycling also disposes of the KOH electrolyte properly, since in large quantities it can cause environmental damage. Large NiMH batteries, such as from EVs or hybrids, should be recycled through vehicle dealers or the original battery suppliers.
LEAD-ACID BATTERIES
1.2.2
Lead. Chemical symbol Pb (from the Latin plumbum). Atomic number 82, atomic weight 207 grams/mol. Lead is an abundant heavy metal, easily and cheaply extracted from ore. It was used by the ancient Egyptians and was widely used for plumbing in the Roman Empire, leading to one of the theories regarding the empire’s collapse.
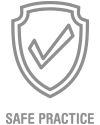
Lead is also poisonous. It accumulates in soft tissues and bones and causes blood disorders and brain damage. Therefore, take all spent lead-acid batteries to a disposal or recycling facility that takes measures to prevent the lead from becoming a future health hazard.
An electrical couple made from lead (as a negative electrode) and lead peroxide (as a positive electrode), using dilute sulfuric acid as an electrolyte, forms a useful secondary battery; in fact, it was the first commercially-developed secondary battery in modern history, invented by Gaston Plant in 1859 (for an interesting ancient possibility, search the internet for Babylonian batteries). The simplified charge and discharge reactions are:
The double-headed arrows indicate that the reactions are reversible. Discharging reads left to right, and charging reads right to left. The ions O– and H+ combine to produce a water molecule. Note that during discharge, both the negative and positive electrodes are converted to lead sulfate. The consequence of this reaction is that the sulfuric acid electrolyte, H2SO4, is “consumed” by discharging, changing into water. There are two undesirable results. The first is that the cell terminal voltage decreases, since the cell voltage is proportional to the concentration of acid. Second, the electrical resistance of the electrolyte increases (acid is a pretty good conductor, but water is a poor conductor), decreasing the available terminal voltage of the cell when load current is flowing. The terminal voltage of the cell drops off slowly at the start of the discharge, but more rapidly toward the end of discharge.
For a deeper look into the reactions, try searching the internet for “lead-acid battery.” Wikipedia and several other internet sites have more information.
The lead-acid battery has miserable energy density by weight, poor energy density by volume, and pretty good power density, due to its ability to deliver high discharge currents. Since the electrolyte is consumed during discharge, the cell has poor voltage regulation (a steep voltage discharge curve). The cell, with a nominal open-circuit voltage of 2.0 V, can’t be discharged below about 0.9 V without risking permanent damage, which would be evidenced by reduced capacity. It has terrible performance at low temperatures and may freeze if fully discharged. Most designs have poor cycle life. Overcharging can release toxic gases, and cause irreversible corrosion of the plates, again reducing capacity. Continuous undercharging can cause irreversible sulfation or hydration, resulting in physical damage to the cell plates. Lead-acid cells have a self-discharge rate of up to 10% per month. Because of the toxicity of lead, battery disposal requires special handling. Recycling is mandatory in most states. Despite all this, the lead-acid battery accounts for 90% of all rechargeable batteries, worldwide, not counting small cells for portable equipment, which are usually NiCd, NiMH or lithium-ion. It’s tough to beat the fact that it’s abundant and … cheaply extracted from ore.
Automotive SLI (starting, lighting, ignition) batteries make up about half of all rechargeable batteries sold. Most are lead-acid. Other major applications for lead-acid include traction batteries (fork lift trucks, golf carts, etc.), telecommunications, switchgear and process controls, and uninterruptible power systems. Smaller batteries are found in emergency lighting and alarms, small vehicles such as scooters and bicycles, and my battery-operated lawn mower.
Because of their poor energy to weight ratio, lead-acid batteries are not likely to find widespread application in electric passenger vehicles. Individuals who build their own electric vehicles generally use lead-acid because of cost and availability. The Chevrolet EV1 initially used a lead-acid battery, but that was replaced by a NiMH battery during manufacture of the second generation of the vehicle.
Remaining sections of this publication are concerned primarily with industrial lead-acid batteries, chiefly stationary batteries.
Construction
1.2.2.1
Pasted-Plate Cell
1.2.2.1.1
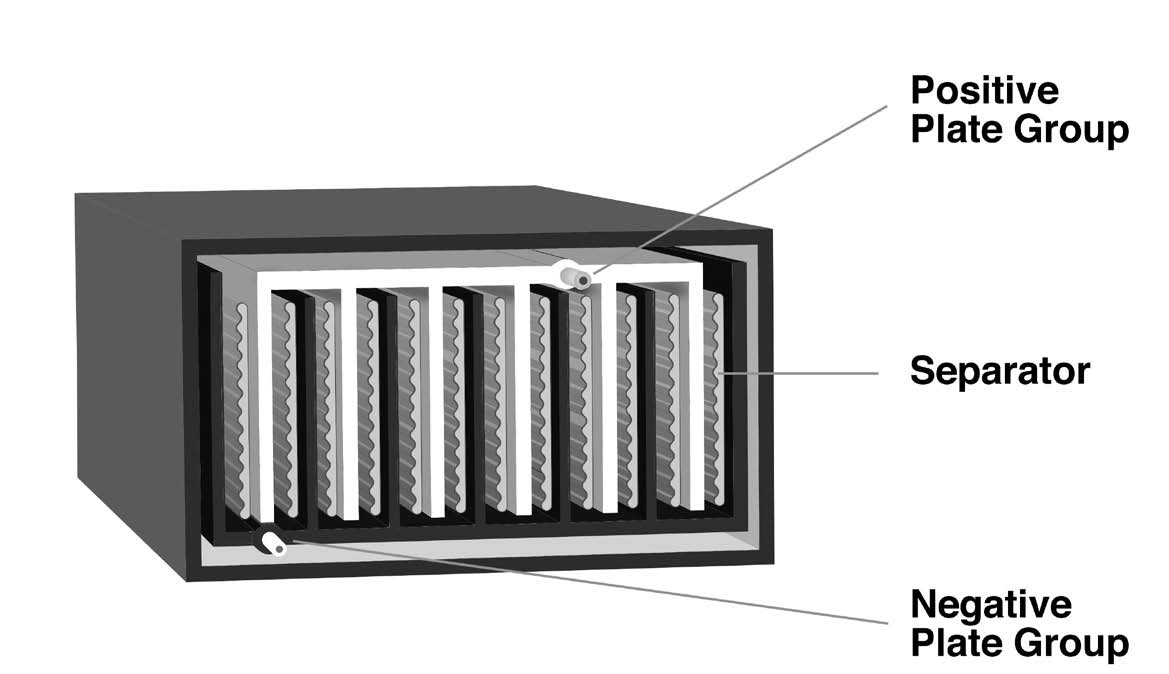
A pasted-plate lead-acid cell (Figure 1b) is made from flat plates of electrode material, with the positive and negative plates stacked alternately in a “jar,” which may be made of glass or plastic. There is always one more negative plate than the number of positive plates; thus, there is always an odd number of plates in a cell. The negative plates are on the outside of the stack of plates at both ends of the jar. The alternating positive and negative plates in a stack are separated by a non-conductive material, such as glass fiber or porous plastic.
A plate consists of a grid cast from molten lead, usually alloyed with another metal to increase its strength. The grid is designed with pockets into which a paste of active material is pressed, resulting in a “pasted-plate” cell. The lead grid isn’t ordinarily involved in charging or discharging the cell; it’s only there to conduct the current in or out and contain the active material.
Various alloys have been developed for manufacturing lead grids. The two most common are antimony (chemical symbol Sb) and calcium (Ca). Lead-antimony grids may also have some selenium in the alloy, which helps to reduce the amount of antimony needed. These cells are frequently marketed as “selenium cells,” and are sometimes called “low-antimony” cells. See the boxout Antimony or Calcium? for more information on their characteristics.
ANTIMONY OR CALCIUM?
Lead is a soft and relatively weak metal and is difficult to cast into grids in pure form. A pure lead grid isn’t strong enough to maintain its geometry in a cell assembly.
Antimony was one of the first metals to be alloyed with lead to form a strong castable alloy. It produces a battery capable of frequent cycling, but because of low gassing voltage, it requires more water addition when used in float service. During float charging, antimony is lost from the grid alloy and expelled as gaseous stibine (antimony hydride), or migrates to the negative plate, causing local discharging. This increases water requirements, and eventually causes grid or plate failure.
Lead-calcium alloys were developed to overcome some of the shortcomings of the antimony alloy, especially high water usage. Because it has higher gassing potential, calcium alloy cells require far less maintenance in float service, but do not cycle well. Calcium alloy grids are used in VRLA batteries and some float service batteries, such as stationary applications. During long-term float service, the calcium is subject to corrosion, which leads to plate failure.
Alloys with low antimony, sometimes with the addition of selenium, overcome the gassing problems of high-antimony alloys, and keep the cycling ability of the antimony alloy. Another alloy is lead-tin, which shows promise for reducing thermal runaway in VRLA batteries.
Internally, each set of plates (positive and negative) is interconnected with lead buses. Each set is then connected to a lead or lead alloy post at the surface of the jar to form the external cell terminal. The jar is filled with a dilute solution of sulfuric acid.
Tubular Construction
1.2.2.1.2
A tubular battery uses a construction different from a pasted-plate battery for the positive plate. The lead grid, instead of having pockets to hold the active material paste, has a row of vertical spines, which are in turn covered with a tube of (usually) glass fiber material. The tube is filled with active material in powder form. The spines make intimate contact with the active material, conducting the current in the same manner as the lead grid in the pasted-plate cell. Because the active material is captive in tubes, rather than being on the surface of flat plates, it’s more resistant to shedding, and the positive plate has a potentially longer life, capable of more charge-discharge cycles. But because the volumetric density is lower, peak current capability isn’t as high as the pasted-plate construction. Manufacturing cost is also higher.
Flooded & Sealed Batteries
1.2.2.2
Traditionally, all lead-acid batteries were “flooded,” (Figure 1c) that is, the plates were immersed in liquid electrolyte, with excess electrolyte above the tops of the plates. During its lifetime, the cell loses electrolyte through evaporation, electrolysis and grid corrosion. The space in the cell above the plates, an electrolyte reservoir, allows the cell to be replenished with water to restore the optimum amount of electrolyte. This obviously requires an access port at the top of the cell, which is normally closed with a vent cap. The vent allows the escape of gas generated during charging. Another name for a flooded cell is vented cell (see the definitions in the Glossary).
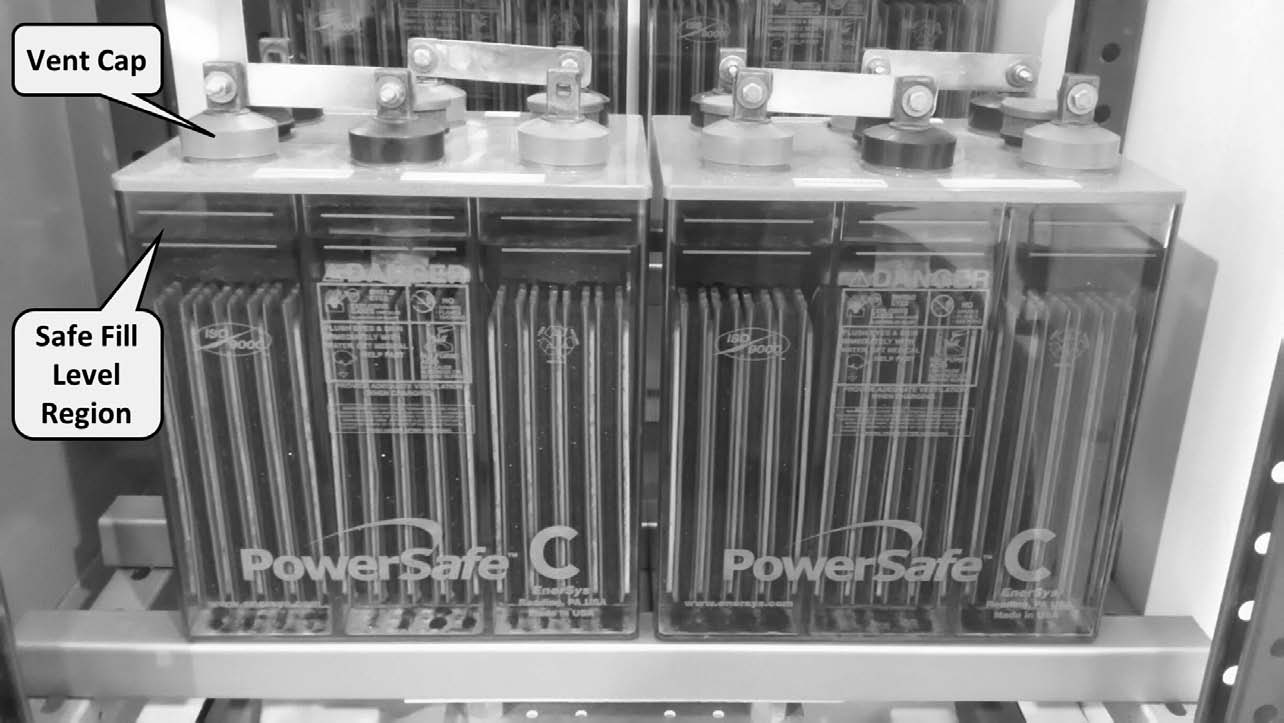
So, if there is a vented cell, there must be an unvented cell, right? Well, yes, relatively speaking. While we haven’t covered charging yet (although you’re welcome to read ahead if you want), you should know that fully charging a lead-acid battery always results in gassing: evolving hydrogen and oxygen by electrolysis. Always. During charging, hydrogen is evolved at the negative plate, and oxygen at the positive.
Since we’re breaking up water, H20, into its constituent gases, hydrogen and oxygen, they’ll be evolved in a stoichiometric ratio. This is about the same as saying “explosive.”
Whether the battery is vented or not, we must make provision for the evolved gases. In a flooded cell, the vent caps usually have flame arrestors. If the gas on the outside of the battery becomes concentrated enough, and is accidentally ignited, the flame arrestor prevents the explosion from propagating to the inside of the cell, and vice-versa.
Now about that unvented cell. The flooded battery requires maintenance, of course. Every so often, you have to “top up” the electrolyte level. A person, at the site, in the battery room. With a big container of water. Someone must clean the tops of the jars, tighten the connections, and if your policy is really ambitious, check the voltage or specific gravity of each cell. With more sophisticated equipment, this person could also check the impedance of each cell, and/or the intercell connection resistances.
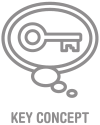
Many users, perhaps including you, would like to reduce that maintenance requirement, especially the part about adding water to the cells. It may take two or three minutes to top off a cell manually, if you do it right. It takes only a few seconds to check the connectors on each cell (be sure to use an insulated wrench).* For you, manufacturers developed “sealed” or “maintenance-free” batteries. Of course, they are neither sealed nor maintenance-free, but they’re a step in that direction. They aren’t truly unvented; the vents are internal, where you normally can’t get at them. In most types, you can’t add water, even if you want to. The correct term is valve-regulated; we’ll use the industry standard abbreviation VRLA, for valve-regulated lead-acid.
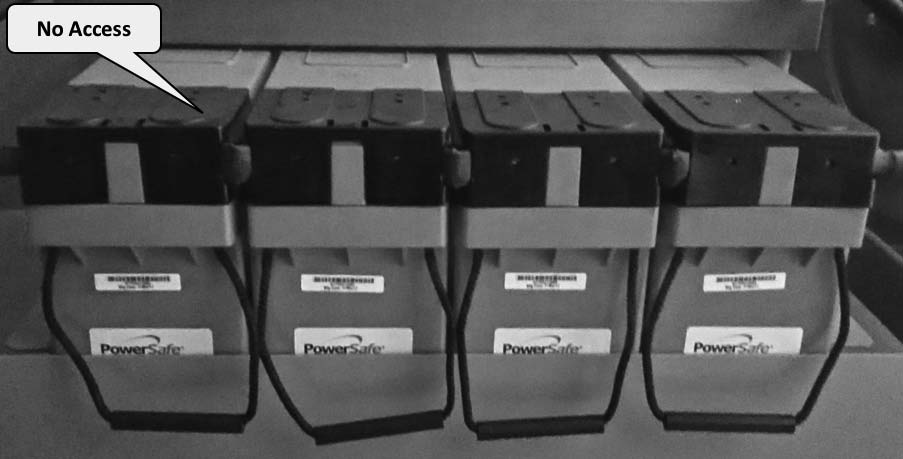
True: VRLA batteries (Figure 1d) are not flooded. They have no external vent caps. They have no electrolyte reservoir. They can be operated on their sides, as well as the normal right-side-up position; some can be operated upside down. Most are classified by the Department of Transportation as “nonspillable,” and are cleared for air transport.
False: VRLA batteries never gas.
Of course, VRLA batteries produce gas during charging. What we need is a means to cope with the evolved gases without letting them escape from the battery. We accomplish this with a vent system designed to seal the battery at atmospheric pressure and slightly above. The cell is constructed so that, at slightly elevated pressures, the evolved gases migrate to the opposite electrode, where by magic they are recombined into water (see the boxout Recombination Magic). If something goes wrong (too much charging current, for example), the cell can vent to release excess pressure, but this inevitably leads to electrolyte loss and reduced capacity. So, to qualify the previous statement that we marked as false, we can say, then, that “VRLA batteries won’t release gas, when operated and charged properly in a controlled environment.”
RECOMBINATION MAGIC
Oxygen at the positive plate migrates to the negative plate, where it reacts with the (sponge lead) active material to produce PbO (lead oxide). In turn, PbO reacts with the electrolyte to make PbSO4 and H2O, restoring the water lost through electrolysis. Float current recharges the PbSO4 back to the sponge lead active material at the negative plate.
Hydrogen evolution at the negative plate is suppressed by the action of the oxygen migrating from the positive. Any excess hydrogen is recombined by a catalyst in the cell. At carefully controlled float charging rates, recombination efficiency is nearly 100%.
In both gel cells and AGM cells, microchannels or pores in the gel or glass fiber separator facilitate the migration of oxygen to the negative plate.
"Gel Cells"
1.2.2.2.1
Gel/Cell (note the forward slash) was originally a trade mark of Globe Union. Today, the generic term gel cell is almost universally used to describe a sealed battery with a gelled electrolyte. Since the electrolyte isn’t a liquid, the cell is very resistant to leakage, and can be operated in any position (although some manufacturers recommend against upside-down operation). Gel cells are very rugged, and capable of moderately high peak discharge currents. The grid alloy is lead-calcium. Because the electrolyte quantity is limited (starved electrolyte) and has less mobility than the free electrolyte in a flooded cell, the cell has some inherent protection against damage from high-rate deep discharges.
AGM (Absorbed Glass Mat) Cells
1.2.2.2.2
Like the gel cell, the AGM cell is virtually leakproof and can be operated in any position. The electrolyte is a liquid absorbed in a glass fiber separator; the plates and separators form a very tight package. This gives the AGM cell the capability for high peak discharge currents and leads to a lower Peukert constant than a gel cell*. Thus, the capacity of an AGM cell decreases less during high rate discharges than does the gel cell. The AGM is also a better performer at low temperatures.
Perfect, right? Well, not exactly. VRLA cells are less tolerant of elevated temperatures than flooded cells. At higher operating temperatures, a temperature-compensated charger is highly recommended (I’d like to say mandatory). Even with temperature compensation, a VRLA cell’s float life will be decreased by about half for each 10 °C above room temperature (a factor that applies to all lead-acid batteries).
Does that reduction in life apply to nickel-cadmium batteries, too?
Yes, but not to the same extent, according to NiCd battery manufacturers. For each 10 °C above room temperature, expect to lose about 20% of the battery’s rated lifetime.
Cylindrical Cells
1.2.2.2.3
Cylindrical lead-acid cells were developed around the 1970s to overcome some of the problems with high-rate discharge at low temperatures. The plates are extremely thin lead-tin alloy, pasted with active material, and then spirally wound with an AGM separator. The sealed, high-pressure vent construction is like small NiCd and NiMH cells. They’re available in standard D sizes and larger, with capacities from a few Ah to a few tens of Ah. They can be used in portable equipment because of their resistance to leakage but are heavier than NiCd or NiMH cells with the same capacity. Lithium batteries will eventually replace most heavy metal batteries in portable applications.
Planté Cells
1.2.2.2.4
The Planté cell design is an attempt to get back to basics — using pure lead as the active material in the positive electrode. A pure lead grid is supported by a structure of lead alloy (usually lead-antimony). The grid is grooved, scored or etched to increase the surface area, or may be cast with openings which are filled with spiral pure lead “rosettes.” The lead plate and/or the lead rosettes are oxidized to lead peroxide during the forming process to produce the positive active material. Plates using the rosette design may be referred to as a Manchester design, or a Manchex™ design (Exide/Hawker trade name).
In a Planté cell of either design, the negative plate is usually the standard pasted-plate design.
The Planté design has very long service life, low self-discharge rate, and relatively low energy density. Because it also has a higher manufacturing cost, it’s best in applications where long unattended float service life is required. Although the Planté design performs well in cycling applications, more maintenance would be required, due to the need for occasional equalization charging (for more on this subject, see SECTION 1.5.5).
LITHIUM SECONDARY BATTERIES
1.2.3
We refer to lithium-ion batteries, rather than pure lithium, when discussing rechargeable lithium systems. Remember that in primary systems, lithium metal is usually used for the anode, and since the lithium is “consumed” during discharge, the reaction is non-reversible. To develop a rechargeable lithium cell, the lithium metal was replaced by an alloy or compound of lithium; as is true for primary cells, there are many competing chemistries. The anode is commonly carbon or a lithium alloy; common cathode materials are lithium cobalt oxide, lithium manganese oxide, and lithium nickel oxide. Lithium ions are “intercalated” in the structure of the anode and migrate to the cathode during discharge. Charging reverses the migration.
Lithium is the lightest solid metal, and the most electrochemically active. It’s an abundant metal, but more expensive to extract from ore than lead because the processes must be non-aqueous and the metal can’t be exposed to air. Lithium ion cells have the highest energy densities, easily four times those of lead-acid or NiCd. Lithium polymer cells, also called lithium ion polymer, have the electrolyte solidified in a polymer; these have extremely high power densities, as well as very high energy densities. Lithium cells also have high open circuit and operating voltages, between 3.5 and 4.0 V for most designs.
The combination of abundant raw materials, light weight, and high energy density makes the lithium secondary battery the obvious choice for the battery of the future. In 2010, the U.S. government began stimulating manufacturing start-up for several companies in the industry with the intent of lowering manufacturing costs and expanding its business potential. Lithium ion’s initial costs to produce in 2016 were still above $500/kWh – more than 4 times the cost of a standard lead-acid flooded battery, and more than 1.5 times the cost of a premium, maintenance-free VRLA gel cell. Now that large scale manufacturing facilities are ramping up production, especially in China, lithium cell cost may decrease to the point where it surpasses lead-acid, not only for applications that require low weight and mobility such as for cellphones, but also for stationary applications discussed in this book.
Lithium batteries are normally not sold as individual cells, but are integrated by the manufacturer in an assembly with protective circuitry, to ensure that the battery always operates within safe voltage and current limits.
Discharge Profile
1.2.3.1.1
The discharge voltage curve has a moderate slope – greater than NiCd, but better than lead-acid. The discharge is normally terminated at 2.5 VPC (volts per cell). Lithium batteries must not be discharged below about 2.0 VPC, or permanent damage will result. The discharge cutoff is usually part of the control circuitry in the battery assembly, which is part of each manufacturer’s battery design. Controlling charge termination also avoids cell reversal.
The discharge voltage is moderately dependent on discharge rate and on temperature (higher with higher temperature), but even at 0 C, the cell voltage is usable. Lithium ion batteries will operate at fairly high temperatures, but most designs are limited to 100 °C. Don’t try that with lead-acid.
Charging Lithium-Ion Batteries
1.2.3.1.2
Recharging the lithium-ion battery requires careful control to keep the battery in the safe operating area. Charging is usually performed with constant current until a critical cell voltage is reached. Charging then continues at that voltage until the charge current drops below a threshold value, typically 3% of the initial charge current. Compared to NiCd or NiMH batteries, lithium-ion batteries have a relatively low self-discharge rate, but an occasional “topping off” charge may be required.
Lithium-ion batteries have no memory effect. Depending on the chemistry used, cycle life can be several hundred to a thousand or more discharge-charge cycles. As the battery ages, the internal impedance rises, and eventually the discharge terminal voltage becomes unusable.
Recycling
1.2.3.1.3
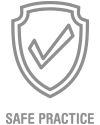
All lithium batteries should be recycled if possible. While lithium isn’t a hazardous waste, many lithium battery types contain some heavy metals (such as cobalt), or other hazardous materials.
OTHER SECONDARY BATTERIES
1.2.4
Nickel-Iron Batteries
1.2.4.1
The NiFe (nickel-iron) battery was commercialized primarily for powering electric vehicles in the early 20th century by Thomas Edison; it became known as the “Edison Battery” although it was invented by Ernst Waldemar Jungner who also brought you the NiCd battery. The anode (negative electrode) is a pocket grid of iron, the cathode is nickel hydroxide, as in the NiCd battery, and the electrolyte is potassium hydroxide.
The major disadvantages to the NiFe battery are low volumetric energy density, low power density, low (and slow) charge efficiency, and high self-discharge rate. It has a high gassing rate during recharging, and therefore requires more maintenance than other secondary batteries. But its great advantages are an extremely long cycle life, high tolerance to abuse, and good high temperature performance. Expected service life is at least 20 years. The anode and cathode active materials are less toxic than those in NiCd and lead-acid batteries.
The NiFe battery is used today in mining and some solar power applications, where its high cycle life is an advantage.
Silver-Cadmium Batteries
1.2.4.2
The silver-cadmium battery substitutes silver oxide for the nickel hydroxide cathode material used in a NiCd battery. Compared to NiCd, the silver-cadmium battery is characterized by higher energy density, higher power density, lower self-discharge rate, equivalent cycle life, and better low- and high-temperature performance.
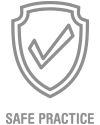
Perfect, right? Not when you consider the cost of silver. Also, they still have environmental problems: silver and cadmium are regulated hazardous waste, according to the EPA. This requires recycling or expensive disposal at the end of life. Batteries containing silver are normally recycled anyway because of cost.
They’re still used in a few NASA and military applications, but they will probably be phased out because of the cadmium content, in favor of silver-zinc, NiMH, or lithium technologies.
Silver-Zinc Batteries
1.2.4.3
Silver-zinc rechargeable batteries are also primarily in use by the military, again because of cost barriers. The silver-zinc battery comprises an anode of zinc, a cathode of silver oxide, and potassium hydroxide as the electrolyte. They have very high energy density compared to nickel technologies, and have higher energy density than lithium ion batteries. But their cycle life is limited by anode dendrite growth, which requires special techniques to control, including the addition of mercury.
Despite their cost, at least one manufacturer has commercialized a silver-zinc secondary battery for hearing aid applications. The manufacturer had tried to develop a larger secondary battery for portable computers, but that effort has apparently been abandoned. Stay tuned.
COMPARING SECONDARY CELLS
1.2.5
Table 1b compares features of commonly available rechargeable battery types.
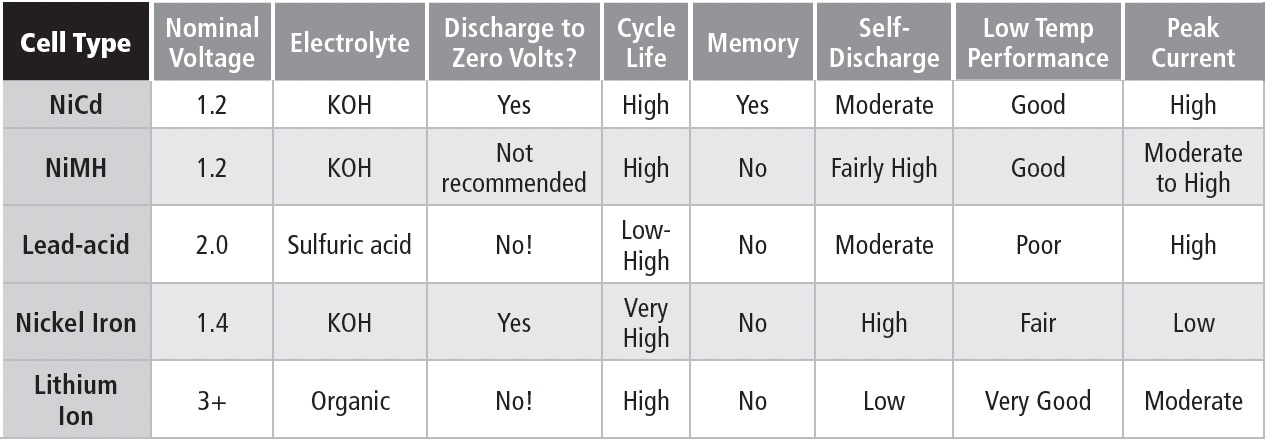