Can I Run A Charger From An Auxiliary Generator?
Part of Chapter Different Charger Applications
A BATTERY CHARGER can be run from a diesel or gas turbine generator that is sized appropriately. You should be aware of performance issues that may affect other equipment running at the same time on the generator. What follows will help you to size a generator successfully.
SIZING THE GENERATOR
7.5.1
Handling the ac inrush current to the battery charger is an important consideration in sizing. The inrush current to a charger can be as high as 15 times the full load operating current, with a typical value of 10 times. When operating from a normal utility source, this magnitude lasts for only one cycle at the line frequency, about 16.7 ms at 60 Hz, and is usually greater in the first half cycle than in the second half cycle. This creates a dc component in the transformer core flux that must be overcome before the steady state is reached (the 15× inrush current specification takes the dc component into account).
The inrush current over subsequent cycles is much lower, and the current rapidly approaches the no-load value, usually within about ten cycles at the line frequency. The no-load value for most transformers is about two to four percent of the full load current. The behavior of a charger is similar, in this respect, to other ac machines, such as a compressor or pump motor.
When you run a charger from a generator, the inrush current is a more complicated issue. The very high, initial, peak inrush-current can easily be provided by a normal utility connection, whose short-circuit current capability can be 22 kA or greater. Even with this capacity during an inrush, the ac voltage at the input terminals of the charger will be depressed by an unpredictable amount, due to the impedances of the utility source, the facility wiring, and the charger’s internal wiring. A good estimate is a 10% reduction in ac voltage at the input terminals for the duration of the inrush.
When a charger is started with a generator, the generator initially sees what looks like a short circuit on its output. A diesel generator might have a much lower fault-current capability than a normal utility, due to the finite reactance of the generator. One manufacturer specifies the sub-transient reactance as that which operates over the first six cycles after a short circuit is encountered. For their products, a reactance as high as 0.17 per unit is possible, but their example calculations use 0.10, which is a more conservative number for circuit breaker coordination.
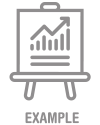
Example: Suppose you are installing a 130 V, 300 A charger to run from a generator. The charger’s normal full-load input current is 81 Aac at 480 Vac. If you obtain a 100 kVA generator at 480 Vac three phase, the generator’s normal full-load output current would be approximately 120 Aac. With a 0.10 per unit reactance, the initial fault current for a short circuit will be about 1,200 Aac. With a full-load rating of 81 Aac, the charger would normally demand an inrush of between 800 Aac and 1,200 Aac. It is important to note, however, that for the first cycle or two, the output voltage of the generator will be near zero because its internal impedance is much higher than that of a normal utility connection. This changes the start-up dynamics: The charger transformer’s inrush current will be lower and will take longer to reach steady state. Settling time cannot be predicted, only measured, and it will vary.
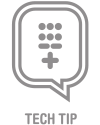
Because of these considerations, we usually recommend that a generator be sized at twice the total input VA rating of the charger. In this example, this would mean a rating of about 150 kVA. We make this recommendation because we expect that other ac loads, besides the charger, will eventually be connected to the generator. If the generator is permanently dedicated to the charger, a lower rating is permissible, and probably is economically more desirable. A generator rating of at least 125% of the charger input VA rating would be satisfactory.